Understanding China Plastic Injection Molding: The Backbone of Modern Manufacturing
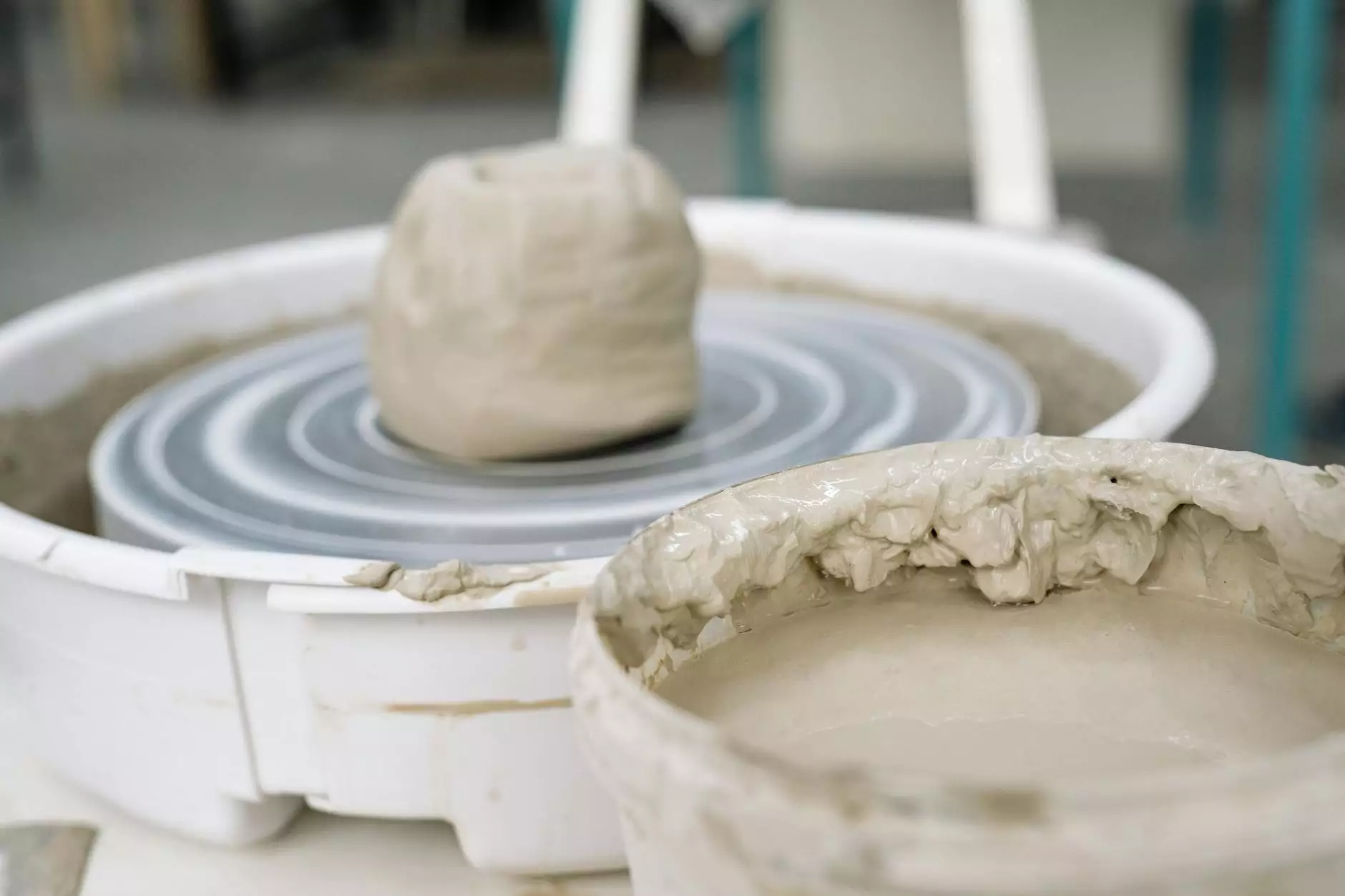
China plastic injection molding has transformed the landscape of manufacturing and is a fundamental part of numerous industries today. Whether it's automotive, electronics, or consumer goods, the usage of plastic components is pervasive, making the injection molding process incredibly important for efficiency and productivity.
The Evolution of Plastic Injection Molding in China
Since its inception in the mid-20th century, plastic injection molding has undergone remarkable advancements. Initially introduced as a novel way to manufacture plastic products, its evolution in China has been nothing short of revolutionary. The country has become a global leader in manufacturing due to its ability to produce high-quality plastic components at competitive prices.
- Growth of the Industry: The rise of China's manufacturing capabilities has positioned it as a dominant force in the production of plastic items.
- Technological Advancements: Innovations in machinery and material science have enhanced the efficiency and precision of injection molding processes.
- Global Demand: With an increasing international demand for plastic products, China has emerged as the go-to destination for businesses seeking reliable manufacturing partners.
What is Plastic Injection Molding?
Plastic injection molding is a manufacturing process for producing parts by injecting molten material into a mold. It's characterized by its efficiency and the ability to produce parts in high volumes. The process involves several key stages:
- Material Preparation: Plastic pellets are fed into the injection molding machine, where they are heated and melted.
- Mold Injection: The molten plastic is injected into a mold cavity, taking the shape of the desired component.
- Cooling: The material cools and solidifies, forming the final product.
- Mold Release: The mold is opened, and the finished part is ejected.
This process enables the production of intricate shapes and designs that may otherwise be challenging to achieve with traditional manufacturing methods.
Advantages of China Plastic Injection Molding
Choosing to manufacture through China plastic injection molding offers several benefits:
1. Cost-Effectiveness
China is known for its competitive pricing in labor and material costs, making it an attractive destination for businesses looking to minimize production expenses.
2. High Efficiency and Speed
The injection molding process is incredibly efficient, allowing for high-volume production that significantly reduces lead times. Once the mold is created, thousands of parts can be produced in a short period.
3. Versatility of Materials
China's advanced technology in plastic processing enables the use of various materials, including thermoplastics, thermosetting plastics, and even specialized materials that meet specific industry standards.
4. Precision and Quality
Modern injection molding machines offer high precision and repeatability, ensuring that every part is manufactured to exact specifications. This is crucial in industries where tolerances are tight, such as aerospace and automotive.
5. Environmental Considerations
With a focus on sustainability, many Chinese manufacturers are adopting eco-friendly practices, including recycling scrap materials and utilizing biodegradable plastics.
The Role of Metal Fabricators in Plastic Injection Molding
While we primarily discuss China plastic injection molding, it is essential to recognize the complementary role of metal fabricators. Metal fabricators provide the necessary molds required for the injection molding process. The relationship between the two sectors is pivotal, as:
- Quality Molds Lead to Better Products: Metal fabricators ensure that molds are made from high-quality steel or aluminum, which significantly affects the longevity and durability of molds.
- Innovation in Design: Collaboration between plastic manufacturers and metal fabricators can lead to innovative mold designs that enhance the molding process.
- Rapid Prototyping: Fabricators provide rapid prototyping services, allowing businesses to test designs before full-scale production begins.
Key Considerations When Choosing a Chinese Injection Molding Partner
Before selecting a manufacturer for plastic injection molding, consider the following factors:
1. Experience and Expertise
Look for a company with a proven track record in plastic injection molding. Examine their portfolio and ask for references to ensure they have the relevant experience.
2. Quality Certifications
Check whether the manufacturing facility holds necessary quality certifications such as ISO 9001, which guarantees adherence to international quality standards.
3. Technological Capabilities
The injection molding industry is ever-evolving. It's crucial to partner with a manufacturer who invests in the latest technology to ensure efficient and high-quality production.
4. Communication and Support
Effective communication is vital for a successful partnership. Choose a company that provides excellent customer support and is responsive to your needs.
The Future of Plastic Injection Molding in China
As we look toward the future, the China plastic injection molding industry is poised for continued growth, driven by several trends:
- Increased Automation: With advancements in technology, the industry will see higher levels of automation, reducing labor costs and improving precision.
- Sustainable Practices: The push for eco-friendly manufacturing will lead to innovations in biodegradable materials and recycling processes.
- Customization and On-Demand Production: As consumer preferences shift toward personalized products, injection molding will adapt to provide more customized options.
Conclusion
The importance of China plastic injection molding in the global manufacturing landscape cannot be overstated. Its benefits—cost-effectiveness, speed, versatility, and quality—position it as a vital manufacturing process for modern industries. As the industry continues to evolve, it remains essential for businesses to stay informed and choose the right partners in this dynamic field.
For businesses looking to thrive in a competitive market, understanding the intricacies of plastic injection molding, as well as the crucial role of metal fabricators, is vital. With the right strategies and partnerships, companies can harness the power of this technology to drive innovation and meet the ever-growing demands of consumers worldwide.